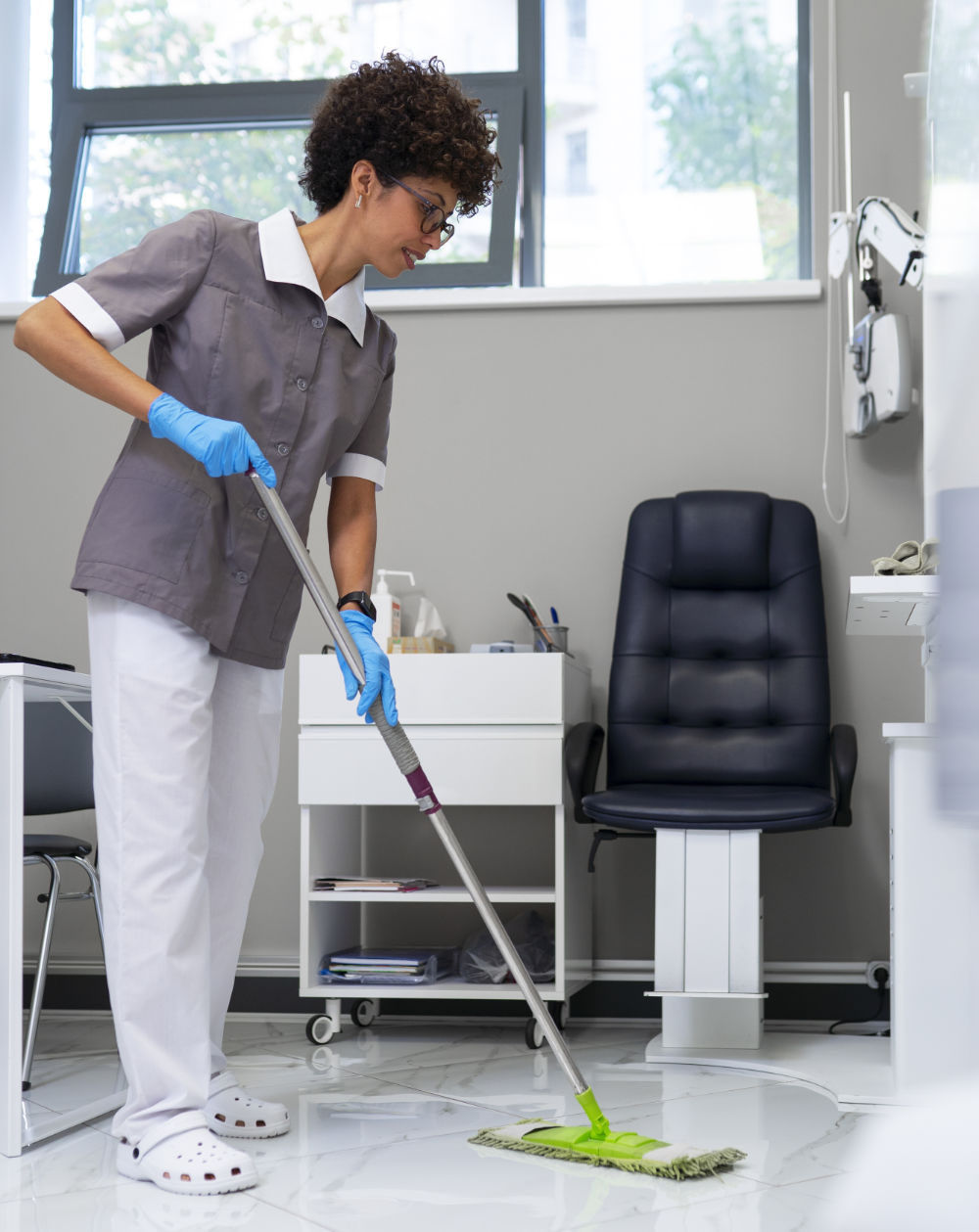
23 Jan Root Cause Analysis in Cleaning Service Failures
When cleaning services fail to meet expectations, there’s often an instinctive rush to address what’s immediately visible—a dirty floor gets mopped again, a missed area gets cleaned, or a complaint gets quickly resolved. This reactive approach, whilst temporarily satisfying, typically leads to a cycle of recurring problems because it focuses solely on visible symptoms rather than understanding why the failure occurred in the first place.
For instance, a repeatedly dirty corridor might be met with multiple re-cleans throughout the day, consuming valuable staff time and resources. However, this approach fails to identify whether the issue stems from inadequate cleaning frequency, inappropriate cleaning methods, insufficient staffing levels, or even building design problems such as poor matting systems that allow excess soil to enter the building.
Root Cause Analysis (RCA) provides a structured approach to breaking this reactive cycle by methodically investigating why cleaning failures occur and how to prevent their recurrence. Rather than simply addressing surface-level issues, RCA delves deeper to uncover the fundamental causes of problems. It might reveal, for example, that a persistent cleaning failure isn’t due to staff negligence but rather to a combination of factors such as poorly maintained equipment, inadequate chemical dilution systems, and unrealistic scheduling.
This systematic method helps facilities managers move beyond quick fixes to implement lasting solutions. By understanding the true nature of cleaning failures, managers can develop targeted interventions that address underlying problems rather than just their symptoms. Such an approach not only improves cleaning effectiveness but also optimises resource utilisation and reduces the frustration of dealing with recurring issues.
Understanding Root Cause Analysis
Root Cause Analysis in cleaning operations involves digging deeper than surface-level problems to identify the fundamental issues that lead to service failures. It’s about asking “why” multiple times until you reach the core of the problem.
The Difference Between Symptoms and Causes
Common symptoms of cleaning failures include:
- Visible dirt or dust
- Customer complaints
- Failed inspections
- Inconsistent results
- Recurring problems in specific areas
However, these symptoms often mask deeper causes such as:
- Inadequate processes
- Equipment limitations
- Staffing issues
- Environmental factors
- Systemic organisational problems
Implementing RCA in Cleaning Operations
Step 1: Problem Identification and Documentation
Begin by gathering detailed information about the cleaning failure:
- Specific location and timing of the issue
- Frequency of occurrence
- Impact on facility users
- Photographic evidence where applicable
- Historical data of similar incidents
Step 2: Data Collection
Collect relevant data from multiple sources:
- Staff interviews and feedback
- Cleaning logs and schedules
- Equipment maintenance records
- Supply usage patterns
- Quality control reports
- Building occupancy data
- Weather records (if relevant)
Step 3: Analysis
The most popular and effective analytical methods can help identify root causes is called the ‘5 Whys’:
The 5 Whys Technique
Start with the problem and ask “why” repeatedly until you reach the root cause. For example:
- Why is the floor dirty? (Because it wasn’t mopped today)
- Why wasn’t it mopped? (Because the cleaner ran out of time)
- Why did they run out of time? (Because they spent too long cleaning another area)
- Why did the other area take so long? (Because the equipment wasn’t working properly)
- Why wasn’t the equipment working? (Because preventive maintenance wasn’t performed)
Step 4: Pattern Recognition
Look for patterns in the data:
- Time-based patterns (specific days or times)
- Location-based patterns (particular areas or surfaces)
- Staff-related patterns (specific shifts or individuals)
- Activity-based patterns (related to building usage)
- Seasonal patterns (weather-related issues)
Common Root Causes in Cleaning Operations
Process-Related Causes
- Inadequate cleaning frequencies
- Improper cleaning sequences
- Unclear standard operating procedures
- Poor quality control mechanisms
- Ineffective scheduling systems
Resource-Related Causes
- Insufficient staffing levels
- Inadequate equipment maintenance
- Poor quality supplies
- Limited storage facilities
- Budget constraints
Management-Related Causes
- Unclear responsibilities
- Poor communication systems
- Inadequate supervision
- Lack of accountability
- Inconsistent standards
Environmental Causes
- Building design issues
- High-traffic patterns
- Weather conditions
- Construction activities
- Building material limitations
Developing Solutions
Once root causes are identified, develop comprehensive solutions:
Short-term Actions
- Immediate procedural changes
- Quick equipment repairs or replacements
- Temporary staff adjustments
- Emergency supply procurement
- Rapid communication updates
Long-term Solutions
- Process redesign
- Equipment upgrade programmes
- Staff development plans
- Facility modifications
- System improvements
Implementation and Follow-up
Creating Action Plans
- Assign responsibilities
- Set timelines
- Allocate resources
- Establish milestones
- Define success metrics
Monitoring Progress
- Regular checks and inspections
- Data collection and analysis
- Staff feedback sessions
- Customer satisfaction surveys
- Performance metrics tracking
Preventing Future Failures
Preventive Measures
- Regular system audits
- Preventive maintenance programmes
- Staff training and development
- Quality control procedures
- Communication improvements
Documentation and Learning
- Record findings and solutions
- Share lessons learned
- Update procedures
- Train staff on new methods
- Create reference materials
Conclusion
Root Cause Analysis in cleaning operations requires dedication and systematic thinking. While it may seem time-consuming initially, it ultimately saves resources by preventing recurring problems and improving overall service quality. By understanding and addressing the true causes of cleaning failures, facilities managers can develop more effective, sustainable solutions that enhance cleaning performance and customer satisfaction.
Success in RCA depends on:
- Commitment to thorough investigation
- Willingness to look beyond obvious answers
- Engagement of all stakeholders
- Systematic documentation and analysis
- Follow-through on identified solutions
When properly implemented, RCA becomes a powerful tool for continuous improvement in cleaning operations, leading to better results and more efficient use of resources.